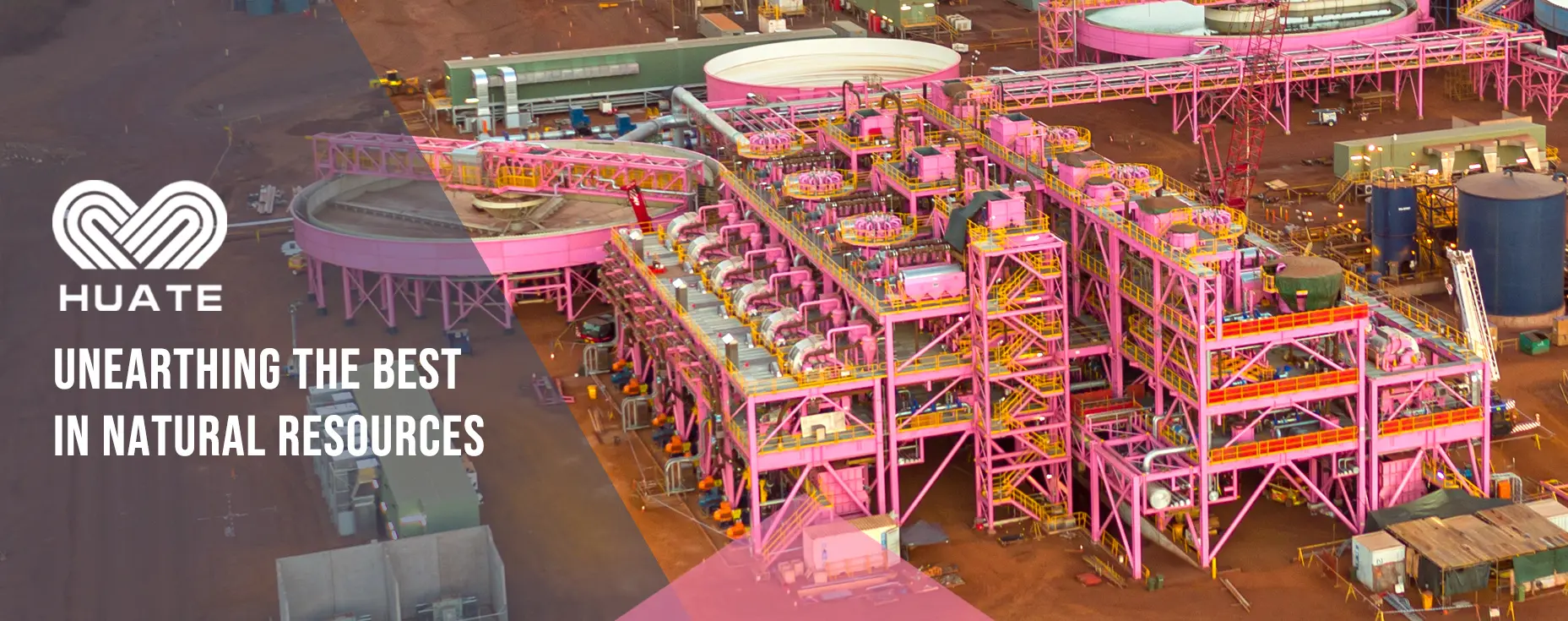
Sendo um dos metais mais antigos e mais utilizados no mundo, o minério de ferro é uma matéria-prima essencial para a produção de ferro e aço.Atualmente, os recursos de minério de ferro estão se esgotando, caracterizados por uma maior proporção de minério pobre em comparação com minério rico, minério mais associado e composições de minério complexas.O ferro é comumente extraído de seu minério, conhecido como hematita ou magnetita, por meio de um processo denominado beneficiamento de minério de ferro.As etapas específicas envolvidas na extração industrial do ferro podem variar dependendo da natureza do minério e dos produtos desejados, mas o processo geral normalmente envolve as seguintes etapas:
Mineração
Os depósitos de minério de ferro são identificados pela primeira vez através de atividades de exploração.Uma vez encontrada uma jazida viável, o minério é extraído do solo por meio de técnicas de mineração, como mineração a céu aberto ou subterrânea.Esta fase inicial é crucial, pois prepara o terreno para os processos de extração subsequentes.
Esmagamento e moagem
O minério extraído é então triturado em pedaços menores para facilitar o processamento posterior.A britagem geralmente é feita usando britadores de mandíbulas ou britadores de cone, e a moagem é realizada usando moinhos autógenos ou moinhos de bolas.Esse processo reduz o minério a um pó fino, facilitando o manuseio e o processamento nas etapas subsequentes.
Separação Magnética
O minério de ferro geralmente contém impurezas ou outros minerais que precisam ser removidos antes de poder ser utilizado na produção de ferro e aço.A separação magnética é um método comum empregado para separar minerais magnéticos de minerais não magnéticos.Ímãs fortes, como o separador magnético Huate, são usados para atrair e separar as partículas de minério de ferro da ganga (materiais indesejados).Esta etapa é crítica para melhorar a pureza do minério.
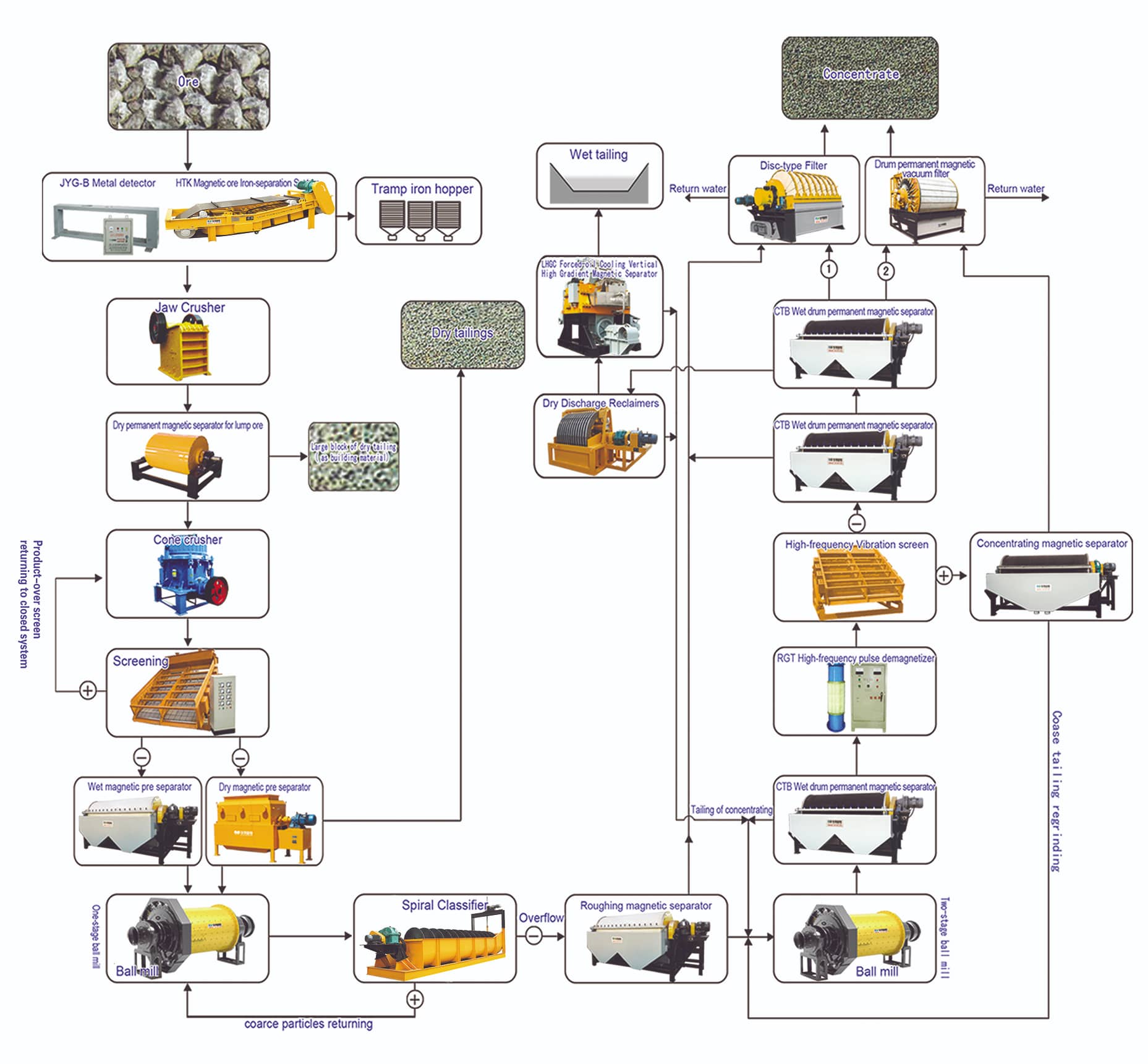
Beneficiamento
A próxima etapa é o beneficiamento do minério, onde o objetivo é aumentar o teor de ferro por meio de diversas técnicas.Este processo pode envolver métodos de lavagem, peneiramento e separação por gravidade para remover impurezas e melhorar a qualidade do minério.O beneficiamento também pode incluir flotação, onde produtos químicos são adicionados ao minério para fazer as partículas de ferro flutuarem e se separarem do resto do material.
Pelotização ou Sinterização
Uma vez beneficiado o minério, pode ser necessário aglomerar as partículas finas em partículas maiores para um processamento mais eficiente.A pelotização envolve a formação de pequenas pelotas esféricas misturando o minério com aditivos como calcário, bentonita ou dolomita.A sinterização, por outro lado, envolve o aquecimento dos finos do minério junto com os fluxos e a brisa do coque para formar uma massa semifundida conhecida como sinter.Esses processos preparam o minério para a etapa final de extração, melhorando suas propriedades físicas e características de manuseio.
Fundição
A etapa final do processo de extração é a fundição, onde o minério de ferro é aquecido em alto-forno junto com o coque (combustível carbonáceo) e o calcário (que atua como fundente).O calor intenso decompõe o minério em ferro fundido, que se acumula no fundo do forno, e escória, que flutua no topo e é removida.O ferro fundido é então moldado em vários formatos, como lingotes ou tarugos, e posteriormente processado para obter os produtos de ferro e aço desejados.
É importante observar que diferentes depósitos de minério de ferro e plantas de processamento podem ter variações nos processos específicos empregados, mas os princípios gerais permanecem semelhantes.A extração de ferro do minério é um processo complexo e de várias etapas que requer uma gestão cuidadosa de recursos e tecnologia.A inclusão de equipamentos avançados como o separador magnético Huate aumenta a eficiência e a qualidade do processo de separação, garantindo que o produto final atenda aos padrões exigidos para a produção de ferro e aço.
Horário da postagem: 08/07/2024